Plastic extrusion for optimized, scalable manufacturing solutions
Key Benefits and Considerations of Carrying Out Plastic Extrusion in Your Projects

Understanding the Essentials of Plastic Extrusion
Plastic extrusion, a staple in the manufacturing industry, is a procedure that involves melting raw plastic product and reshaping it into a continual profile. This profile, once cooled, can be reduced right into desired sizes or curled for later use. The charm of plastic extrusion depends on its versatility. A wide variety of items, from piping to window frames, can be created. The process needs an extruder, a complex maker with a warmed barrel, a turning screw, and a die at the end. The plastic product, in the form of pellets, is fed into the extruder, where it's thawed and required through the die, taking its form. The choice of plastic and the style of the die figure out the item's features.
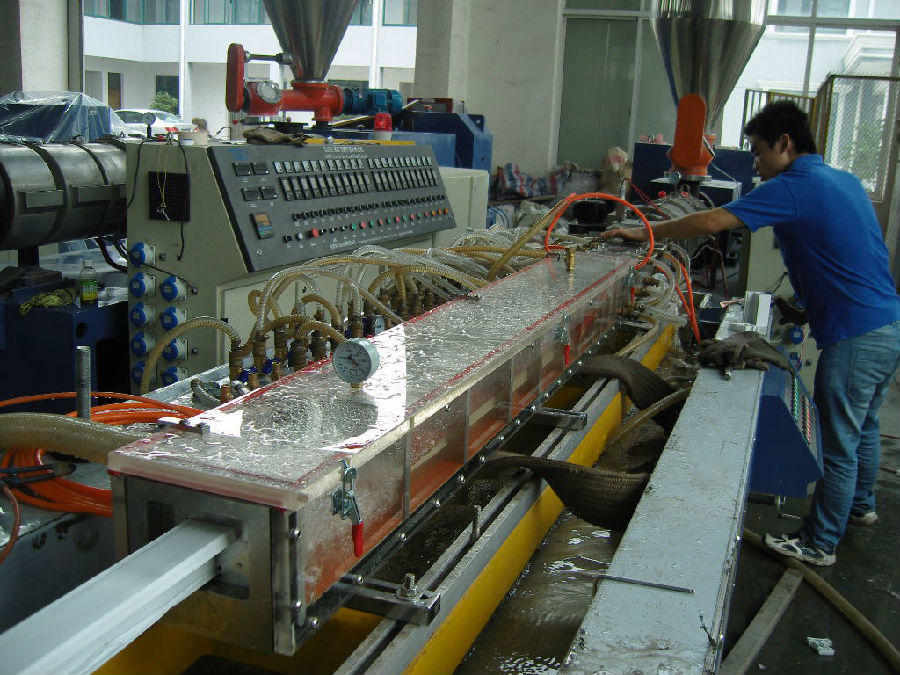
The Economic Benefit of Plastic Extrusion
The economic benefit of plastic extrusion exists predominantly in two locations: cost-efficient material manufacturing and advantageous production rates. With plastic extrusion, companies can produce high quantities of product at a reduced cost compared to various other methods. The procedure flaunts an outstanding production rate, considerably reducing time and further boosting its economic feasibility.
Affordable Material Production
A substantial advantage of plastic extrusion is its impressive cost-effectiveness. This manufacturing procedure permits continual, high-volume production with very little waste, which equates into lower prices. The raw products made use of, usually plastic pellets, are fairly cost-effective compared to other substances (plastic extrusion). The process itself requires much less energy than lots of various other manufacturing techniques, even more lowering prices. In addition, the extrusion procedure enables a high level of accuracy fit the plastic, minimizing the requirement for costly post-production changes or improvements. In addition, the longevity and long life of extruded plastic products typically imply less need for replacements, adding to long-lasting cost savings. All these variables make plastic extrusion an extremely economical selection for several jobs, providing an attractive equilibrium in between expense and performance.
Beneficial Production Speeds
While keeping the cost-effectiveness of the products, an additional notable benefit of plastic extrusion hinges on its fast production rates. This performance in the manufacturing procedure is associated to the constant nature of the extrusion procedure, permitting high-volume production in a reasonably brief time span. The speed of manufacturing straight correlates to a decline in labor expenses and a boost in result, thus improving the total financial feasibility of the procedure. Furthermore, the fast-paced manufacturing does not endanger the top quality of the end product, making certain trustworthy and consistent results. This mix of speed, cost-effectiveness, and quality underscores the significant financial benefit of applying plastic extrusion in numerous tasks.
Flexibility and Customization: The Strengths of Plastic Extrusion
One of the noticeable strengths of plastic extrusion depends on its versatility and customization possibility. These high qualities unlock to unlimited design opportunities, giving makers the capacity to customize items to particular requirements. This enhanced level of personalization not just boosts item performance but also significantly enhances product individuality.
Unrestricted Layout Possibilities
Plastic extrusion radiates in its capacity to supply virtually unlimited layout opportunities. Plastic extrusion can take care of a selection of plastic kinds, expanding its application scope. With plastic extrusion, the design possibilities are practically unlimited.
Increasing Item Uniqueness
The adaptability of plastic extrusion can substantially boost item originality. This procedure permits developers to explore different forms, sizes, and colors, giving them the freedom to develop unique products that attract attention in the market. It is this customization that provides a distinctive identification to each product, differentiating it from its competitors.
In addition to its aesthetic benefits, the customizability of plastic extrusion likewise provides useful benefits. Developers can customize the buildings of the plastic according to the details demands of the application, improving the product's capability. They can make the plastic a lot more flexible, extra long lasting, or much more immune to heat, depending on what the item requires. Hence, plastic extrusion not only boosts item individuality however also its energy and marketability.
Layout Limitations in Plastic Extrusion: What You Need to Know
How can design constraints potentially impact the procedure of plastic extrusion? While plastic extrusion is versatile, layout restrictions can cut its advantages. Specific complicated designs may not be viable because of the restrictions of the extrusion procedure, potentially limiting the creation of elaborate accounts. The use this link procedure is much less appropriate for hollow or multi-chambered frameworks. In addition, the extrusion procedure may not always offer the preferred surface area coating, especially for those requiring high gloss or optical clearness. Product option can also pose difficulties, as not all polymers are suitable for extrusion. High-temperature resistant plastics, for instance, may provide troubles. Comprehending these restrictions is essential for reliable execution of plastic extrusion in your jobs. plastic extrusion.
Reviewing the Ecological Influence of Plastic Extrusion
While recognizing layout constraints is a substantial aspect of plastic extrusion, it is just as vital to consider its ecological ramifications. The procedure of plastic extrusion involves melting plastic materials, potentially launching unsafe gases into the environment. Further, the resulting items are typically non-biodegradable, adding to garbage dump waste. Nevertheless, developments in technology have actually permitted more environmentally-friendly practices. As an you could try this out example, using recycled plastic products in the extrusion procedure can minimize environmental influence. In addition, establishing biodegradable plastic choices can help alleviate waste issues. Evaluating these ecological aspects is important when implementing plastic extrusion tasks, guaranteeing an equilibrium in between performance, cost-effectiveness, and environmental obligation.
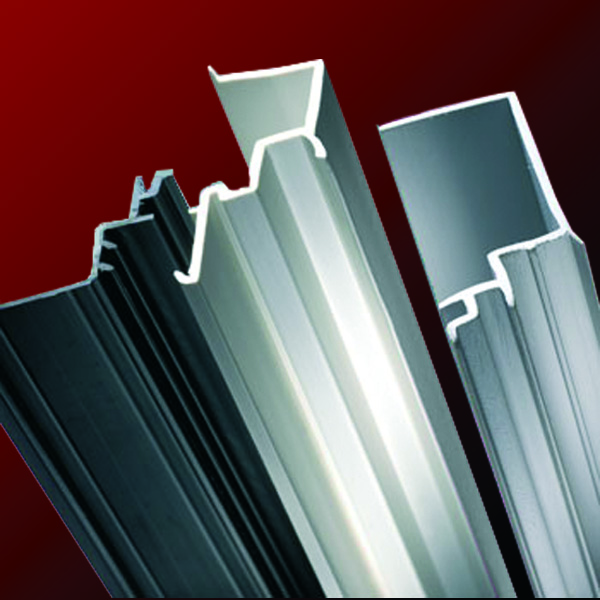
Study: Effective Projects Making Use Of Plastic Extrusion
Success stories in the area of plastic extrusion abound, showing both the versatility and efficiency of this production procedure. One notable example is the creation of PVC pipelines utilized in contemporary plumbing. This process involves melting plastic and forming it into a continual tube, supplying substantial price and durability advantages. One more effective situation is the production of plastic film for packaging and agriculture. With extrusion, makers can create extremely customizable, thin, and durable films. Automotive markets likewise benefit, making use of extruded plastic for components like trim or seals, boosting vehicle long life. These circumstances show plastic extrusion's vital function in different markets, vouching for its versatility, cost-effectiveness, and reputable outcome.
Verdict
In conclusion, plastic extrusion uses a affordable and efficient method for creating intricate forms with minimal waste. Including plastic extrusion into jobs can lead to successful end results, as shown by many case research studies.
Plastic extrusion, a staple in the production sector, is a procedure that entails melting raw plastic material and improving it right into a continuous profile. Plastic extrusion can deal with a range of plastic kinds, broadening its application range.Exactly how can create constraints possibly impact the helpful site procedure of plastic extrusion? The procedure of plastic extrusion entails melting plastic products, possibly launching harmful gases into the environment. Using recycled plastic materials in the extrusion procedure can minimize environmental impact.